Heiß geformt – stabil gebaut!#
von
Ralf Kolleck
Institut für Werkzeugtechnik und spanlose Produktion
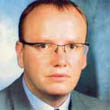
Ralf Kolleck ist Leiter des Instituts Werkzeugtechnik und spanlose Produktion, Member of Frank Stronach Institute [FSI] an der TU Graz. Die praxisrelevanten Forschungsaktivitäten fokussieren sich u.a. auf die Optimierung von Umformprozessen und Umformanlagen, oder die Entwicklung und Verbesserung von Werkzeugsystemen.
© Forschungsjournal 2009/02
Sicher, leicht und zum Design passend: An Fahrzeugkarosserien werden unterschiedlichste Ansprüche gestellt, die sich oft schwer miteinander vereinbaren lassen. Mit höherfesten Blechwerkstoffen wird diesen Anforderungen begegnet – sie stellen allerdings die Umformtechnik vor große Herausforderungen. In diesem Spannungsfeld arbeitet das Institut für Werkzeugtechnik und spanlose Produktion.
Das Institut für Werkzeugtechnik und spanlose Produktion, im Englischen Tools and Forming – kurz T&F, feierte in diesem Jahr bereits seinen fünften Geburtstag. Seit der Institutsgründung imJahr 2004 stieg die Zahl der Mitarbeiterinnen und Mitarbeiter kontinuierlich auf heute 27. Als wichtiger Meilenstein kann der Bezug der eigenen Büro und Laborräume im Jahr 2006 gesehen werden. Das Institut ist im Frank Stronach Institute an der Einfahrt zum Campus Inffeldgasse angesiedelt und ist stolz auf seine hochmodere Ausstattung, die sowohl der anwendungsorientieren Industrieforschung als auch der Grundlagenforschung gerecht wird. Die Forschungsfelder reichen von der Untersuchung von Umformprozessen über die Auslegung von Umformwerkzeugen bis hin zur Optimierung von Maschinen und Anlagen. Um die Studierenden möglichst früh mit der Praxis in Berührung zu bringen, werden diese von Beginn an stark in aktuelle Forschungsprojekte eingebunden. Gerade bei Kooperationsprojekten mit der Industrie besteht hier für beide Seiten, Studierende wie Auftraggeber, die Möglichkeit sich persönlich kennenzulernen. So kann sich schon während des Studiums der Kontakt zu einem zukünftigen Arbeitgeber ergeben.
Heiß geformt – stabil gebaut
Die passive Sicherheit von Fahrzeugen hat in den letzten Jahren enorm zugenommen. Ein moderner Kleinwagen bietet im Falle eines Unfalls deutlich bessere Überlebenschancen für die Insassen als ein 20 Jahre altes Mittelklassemodell. Grund hierfür ist der Einsatz von höchstfesten Blechwerkstoffen. Hohe Sicherheit und dabei so leicht wie möglich lautet die Devise. Dies wird durch eine Erhöhung der Werkstofffestigkeit bei gleichzeitiger Reduzierung der Blechdicke erreicht. Der Vorteil des "starken Stahls" ist aber gleichzeitig ein Problem: Durch die extreme Materialhärte wird das Zuschneiden der Blechteile zu einer echten Herausforderung.
Hochfester Stahl kann zudem nicht mit den gewohnten "kalten" Umformvorgängen in Form gebracht werden, er würde aufspringen und sich verdrehen. Am problemlosen Zuschneiden der Bleche wird noch eifrig geforscht, der anderen Zwickmühle bietet das Institut für Werkzeugtechnik und spanlose Produktion mit dem so genannten Presshärten die Stirn. Dabei wird das Blech auf etwa 950°C erhitzt, durch eine Matrize in Form gepresst und sofort wieder auf 190°C abgekühlt.
Hierdurch erhält das fertige Bauteil eine extrem hohe Festigkeit. Da die Erwärmung des Blechs in der industriellen Anwendung einen hohen technischen Aufwand mit sich bringt, wurde am Institut eine für diesen speziellen Anwendungsfall einzigartige Induktionsanlage entwickelt, die die Wärme direkt in das Blech leitet und so deutlich weniger Energieverluste aufweist. Die Blechumformung gestaltet sich durch die gezielte Wärmeabgabe nicht nur um einiges wirtschaftlicher, sondern bringt auch bessere Bauteileigenschaften mit sich.
"Verrückte" Ideen als Impulsgeber
Unsere Aufgabe als Institut ist es, neue Ideen zu entwickeln und die Forschung mit Impulsen voranzutreiben. Es macht wenig Sinn, sich in Details zu verlieren und damit den Blick für das Ganze zu verlieren. Für Innovationsführerschaft müssen wir industrietaugliche Ergebnisse an realen Bauteilen präsentieren und prozesssichere Technologien entwickeln.
Dennoch benötigen wir Freiraum, um auch zunächst verrückt erscheinende Ideen aufgreifen zu können und sie in Grundlagenuntersuchungen auf ihre Machbarkeit hin zu überprüfen. Dieses Wechselspiel zwischen Anwendungs- und Grundlagenorientierung hat dazu geführt, dass sich das Institut bereits in der kurzen Zeit seines Bestehens einen festen Platz in der internationalen Forschungslandschaft erarbeiten konnte. Diesen Platz gilt es in den nächsten Jahren zu festigen und weiter auszubauen.