Mähdrescher
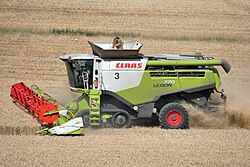
Ein Mähdrescher ist eine landwirtschaftliche Erntemaschine, die entwickelt wurde, um die Ernte und Verarbeitung von Getreide wie Weizen, Gerste, Roggen, Hafer oder Mais effizienter zu gestalten. Der Name setzt sich aus den Wörtern „Mähen“ und „Dreschen“ zusammen, da der Mähdrescher beide Arbeitsschritte kombiniert. Das Getreide wird von Spreu, Stroh und anderen Verunreinigungen getrennt und die sauberen Samenkörner werden in einem eingebauten Korntank gesammelt. Das übrige Stroh wird gehäckselt und gleichmäßig auf dem Feld verteilt oder in Schwaden gelegt, um später für andere Zwecke wie Einstreu oder Naturdüngung genutzt zu werden. Im Vergleich zur manuellen Arbeit können mit einem Mähdrescher große Flächen in kurzer Zeit bearbeitet werden. Der erste selbstfahrende Mähdrescher wurde gegen Ende des 19. Jahrhunderts entwickelt.
Beschreibung der Baugruppen

1) Haspel 2) Messerbalken 3) Einzugsschnecke 4) Schrägförderer 5) Steinfangmulde 6) Dreschtrommel 7) Dreschkorb |
8) Hordenschüttler 9) Stufenboden 10) Gebläse 11) Obersieb 12) Untersieb 13) Überkehrschnecke 14) Überkehr |
15) Kornschnecke 16) Korntank 17) Strohhäcksler 18) Fahrerkabine 19) Motor 20) Abladeschnecke 21) Wendetrommel |
Erntevorsatz
Vorne am Mähdrescher ist der Erntevorsatz. Je nach Art der Druschfrüchte kommen verschiedene Aggregate zum Einsatz. Wenn der Vorsatz breiter ist als drei Meter (Arbeitsbreiten von fast 15 Meter für Getreide und 12 Meter für Mais sind möglich), muss der Vorsatz für die Straßenfahrt entweder abgebaut oder (hydraulisch) zusammengeklappt werden. Das Schneidwerk wird dann mit einem Schneidwerkswagen transportiert.
Schneidwerke

Ein Schneidwerk besteht aus dem Schneidtisch sowie Halmteilern, welche die Getreidehalme der zu mähenden Bahn von dem noch stehen bleibenden Getreide abteilen, gegebenenfalls Ährenhebern, die liegende Getreidehalme (Lagergetreide) unterfahren und aufrichten sollen, der der Zuführung der Getreidehalme zum Balkenmähwerk dienenden Haspel[1], dem Fingermähwerk und der Einzugsschnecke bzw. dem Förderband, die das Schnittgut dem Dreschwerk zuführen.
Rapsvorsatz
Bei der Ernte von Raps werden zur Trennung der Schnittbahnen an den Seiten des Schneidwerkes seitlich senkrecht stehende Scherenschnittmesser angebaut und der Schneidtisch wird verlängert. Raps fällt sehr leicht aus den Samenständen heraus, und die sich verzweigenden Einzelpflanzen verhaken sich miteinander. Durch ein Auseinanderreißen der untereinander verworrenen Rapspflanzen käme es zu erheblichen Kornverlusten. Die Verlängerung fängt die Samen auf, die von der Haspel ausgeschlagen werden.[2] →Rapstrenner
Maisschneidwerke

Maispflücker oder Maisgebisse sind so konzipiert, dass die Pflanzenstängel bei der Überfahrt durch einen schmal zulaufenden Spalt gezogen werden. Die Spaltbreite des Maisschneidwerks sollte dabei möglichst genau dem Durchmesser des Maisstängels entsprechen. Je nach System erfolgt die Einstellung der Spaltbreite manuell vom Führerhaus oder automatisch durch die jeweilige Reiheneinheit.[3] Bei richtiger Einstellung der Spaltbreite wird lediglich die Maispflanze durch den Spalt gezogen, während der breitere Maiskolben von der Pflanze separiert wird. Dieser verbleibt dadurch oberhalb des Schneidwerks und wird anschließend mithilfe der Förderketten sowie der Förderschnecke dem Schrägförderer des Mähdreschers zugeführt. Gleichzeitig zerkleinert ein unter dem Tisch angebrachtes Häckselwerk die Restpflanze. Für Getreide gibt es außerdem Ährenstripper oder auch nur Stripper genannt. Sie arbeiten nach demselben Prinzip wie Maispflücker. Von Vorteil ist, dass das Stroh nicht durch die Maschine muss und sich somit die Stundenleistung des Mähdreschers erhöht.
Sonnenblumenschneidwerke
Beim Drusch von Sonnenblumen werden die Blütenstände vom Stängel getrennt. Vom Aufbau ähneln Sonnenblumenschneidwerke den Maisschneidwerken.
Pickup
Bei ungleichmäßig abreifenden Beständen wird die Frucht zunächst mit einem Schwadmäher abgemäht und auf Schwad abgelegt. Nach weiterem Abreifen der Frucht im Schwad nimmt der Mähdrescher sie mit einer Pickup zum Drusch auf.
Schrägförderer
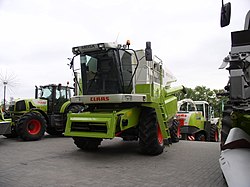
Der Schrägförderer, auch als Schacht bezeichnet, fördert das Erntegut in die Maschine. Innen läuft eine Einzugskette, die das Erntegut von der Einzugsschnecke übernimmt und es dem Dreschaggregat zuführt.
Steinfangmulde
Unmittelbar am Ende des Schrägförderers befindet sich eine Steinfangmulde. Die Dreschtrommel soll die schwereren Steine dort hineindrücken. Da Rotormähdrescher besonders empfindlich auf eingezogene Steine reagieren, gibt es Systeme, bei dem die Steine durch Klopfsensoren erkannt werden und sich bei Steinerkennung der Boden des Schrägförderers öffnet, so dass der Stein wieder auf den Boden gelangen kann.
Dreschorgan
Das Dreschorgan besteht aus einem Dreschkorb, in dem sich entweder eine Dreschtrommel oder ein Rotor mit hoher Geschwindigkeit drehen. Der Spalt zwischen Trommel/Rotor und Korb ist sehr eng. So wird das Korn aus dem Stroh ausgerieben und fällt durch die Maschen des Korbes. Etwa 90 % der Körner werden durch das Dreschaggregat vom Stroh getrennt und gelangen direkt in die Reinigung, lediglich das Stroh und darin noch enthaltenes Restkorn gelangen zur Abscheidung. Je nach Art der zu dreschenden Frucht kann über die Variation der Trommeldrehzahl und eine Veränderung des Dreschspaltes zwischen Dreschtrommel und Dreschkorb die Intensität des Druschs variiert werden.
Noch intensiveres Dreschen kann durch Verschließen der ersten Korbreihen, oder durch den Einbau von Reibleisten erreicht werden. Das ist notwendig, wenn Grannen von Gerstenkörnern abgebrochen werden sollen oder wenn Früchte gedroschen werden, bei denen die Samen sehr fest in den Blütenständen sitzen. Die Abscheidefläche des Korbes verringert sich dabei.
Abscheidung
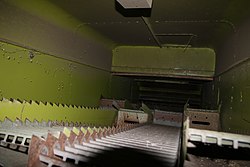
Vom Dreschaggregat gelangt das Erntegut zur Abscheidung, wo die restlichen Körner und nicht vollständig ausgedroschene Ähren vom Stroh getrennt werden. Es gibt verschiedene Abscheidesysteme:
Das klassische Abscheidesystem ist der sogenannte Hordenschüttler (siehe Bild rechts). Dieser besteht aus mehreren versetzt an einer Kurbelwelle befestigten ca. 20 cm breiten sägezahnförmigen Rinnen, über die das Gut aufgrund der Schüttelbewegung nach hinten wandert, wobei das leichtere und sehr viel größere Stroh den ansteigend verlaufenden Schüttlern folgt. Die Körner und nicht vollständig ausgedroschene Ähren werden vom Stroh getrennt und fallen durch kleine Löcher in den Horden in die Schüttlertaschen und rutschen auf das Reinigungssieb.
Ein weiteres Abscheidesystem ist das axiale System. Die Abscheidung erfolgt mit einem oder zwei längs (axial) eingebauten Rotoren, deren Funktionsweise einem Separator ähnelt. Unterhalb der Rotoren ist ein Korb (ähnlich dem Dreschkorb) angebracht, der das Stroh führt, bis es vom Rotor nach hinten aus dem Mähdrescher oder auf den Häcksler gelangt.
Reinigung
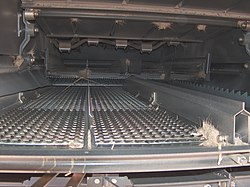
Das Reinigungsgut, bestehend aus Körnern und NKB (Nicht-Korn-Bestandteile = Spreu und Strohteile), gelangt vom Dreschwerk und weiteren Abscheideorganen (Schüttler oder Abscheiderotoren) zur Reinigung. Die Reinigung dieses Gemisches erfolgt in der Regel über zwei übereinander angeordnete Siebe, das Ober- und das Untersieb. Die Zuführung des Reinigungsgutes zu den Sieben erfolgt je nach Hersteller unterschiedlich:
a) Über einen Stufenboden (treppenförmiges Profilblech), der sowohl für die Förderung, als auch für eine gleichmäßige Verteilung in Längs- und Querrichtung und eine gewisse Vorentmischung zuständig ist. b) Über eine aktive Förderung mittels mehreren nebeneinander liegenden Schnecken, deren Hauptaufgabe darin besteht, innerhalb der Reinigung an Höhe zu gewinnen und das Reinigungsgut gleichmäßig den Sieben zuzuführen. c) Eine oder mehrere, mit Hilfe eines Gebläses, belüftete Fallstufen, die bereits vor Erreichen der Siebe einen großen Anteil der leichten Spreuanteile aus dem Reinigungsgut ausblasen. Damit wird vor allem erreicht, dass die Körner unter den NKB auf die Siebfläche auftreffen und zügig abgeschieden werden.
Beide Siebe werden von unten durch einen Luftstrom (Wind) belüftet. Dies sorgt für eine Auflockerung des Reinigungsgutes, wobei im günstigsten Fall eine so genannte Wirbelschichtphase entsteht. Dabei „schwimmen“ leichte Anteile wie die Spreu und Kurzstroh auf und ermöglichen den wesentlich schwereren Körnern das Erreichen der Siebfläche.
Das Reinigungsgut gelangt von der Zuführung aus zunächst auf das Obersieb. Dieses hat im Wesentlichen die Aufgabe, Körner und unausgedroschene Ährenteile (Überkehr) zum Untersieb abzuscheiden und die NKB über das Siebende aus dem Mähdrescher zu fördern. Das Untersieb stellt die letzte Reinigungsstufe dar, wobei im Idealfall eine Kornreinheit von über 99,6 % erreicht wird. Das Reinkorn wird über eine Schnecke zu einer Maschinenseite (in der Regel in Fahrtrichtung rechts) und von dort mittels eines Elevators in den Korntank gefördert. Der Siebübergang des Untersiebes (Überkehr) besteht aus unausgedroschenen Ährenteilen, Körnern und Spreu. Diese Überkehr wird mit einer Schnecke zu einer oder beiden Seiten des Mähdreschers gefördert und von dort mit Hilfe einer weiteren Schnecke oder eines Elevators zum Dreschwerk oder den Förderelementen der Reinigung zurückgefördert. Hersteller, die die Überkehr zur Reinigung zurückführen, bauen auf dem Weg dorthin ein zusätzliches kleines Dreschorgan ein.
Da mit den NKB auch große Mengen an Unkrautsamen aus dem Mähdrescher gelangen, wird die Spreu ebenso wie das Stroh (sofern gehäckselt) bei Schnittbreiten über 3 Meter möglichst über die gesamte Arbeitsbreite verteilt, beispielsweise mittels scheibenförmiger Spreuverteiler. Durch Wechsel von Ober- und Untersiebbauarten sowie durch Variation der Windgeschwindigkeiten kann die Reinigung auf die zu dreschende Getreideart eingestellt werden. Sowohl die Frequenz als auch die Amplitude der Siebschwingung werden meist vom Hersteller vorgegeben und können nur mit großem Umbauaufwand geändert werden.
Korn- und Strohmanagement
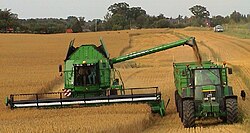
Der Getreidetank dient als Vorratsbehälter für das Korn und hat ein Fassungsvermögen je nach Größe des Mähdreschers zwischen 5 und 18 Kubikmetern. Er ist im Allgemeinen so bemessen, dass Getreide 15–30 min lang ohne Entleerung des Tanks gedroschen werden kann. Anschließend wird das Korn, oftmals auch parallel zum Drusch, über das Abtankrohr auf einen Transportanhänger oder einen Überladewagen entladen. Dabei schaffen leistungsstarke Maschinen wie der AGCO Ideal 9 PL bis zu 210 l/s[4]. Damit kann der komplett gefüllte Korntank in unter 100 Sekunden entleert werden.
Am hinteren Ende des Mähdreschers, hinter den Dresch- und Abscheideorganen, wird das gedroschene Stroh aus dem Mähdrescher ausgeworfen. Das Stroh kann entweder zur späteren Bergung mit einer Ballenpresse auf Schwad gelegt oder gehäckselt werden. Zur Schwadablage verfügen Mähdrescher vielfach über Leitbleche oder Zinken, mit denen sich die Schwadbreite verstellen lässt, um diese auf die Presse anzupassen. Häufig ist bei neueren Maschinen ein Strohhäcksler montiert, der das gedroschene Stroh klein häckselt und es über die gesamte Schnittbreite verteilt. Das gehäckselte Stroh kann später in den Boden eingearbeitet werden und trägt so zur Erhöhung des Humusanteils bei. Bei immer größeren Schnittbreiten stellt eine gleichmäßige Strohverteilung heute eine große Herausforderung für die Hersteller dar.
Motor
Mit einer Nennleistung von 581 Kilowatt (790 PS) gilt der Claas Lexion 8900 derzeit als der Mähdrescher mit der höchsten Motorleistung[5]. Moderne Mähdrescher benötigen die Leistung vor allem für das Dreschaggregat, die Abscheideorgane und den Strohhäcksler. Abhängig von den Erntebedingungen und der Arbeitsbreite verbraucht alleine der Häcksler bis zu 20 % der verfügbaren Leistung. Da während des Dreschens sehr viel Staub entsteht, ist die Zuführung der Verbrennungs- und Kühlluft des Motors problembehaftet. Luftfilter und Kühler müssen daher durch maschinelle Einrichtungen sauber gehalten werden, was entweder mittels einer Absaugung, rotierender Bürsten oder durch ein Lüfterwendegetriebe geschieht. Das Wendegetriebe verändert die Drehrichtung des Kühlerventilators ab einer bestimmten Temperatur kurzzeitig, so dass dieser den Kühler frei bläst.
Fahrwerk
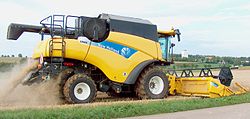

Die ganze Maschine sitzt auf einem Fahrwerk, das von zwei großen und breiten Rädern (oft mehr als 80 cm breit) direkt hinter dem Schneidwerk und unterhalb der Kabine dominiert wird. Gelenkt wird über die hinteren, kleineren Räder. Beim Einsatz in schwierigem Gelände kommen Allradantriebe und auch vermehrt Raupenlaufwerke zum Einsatz, deren Vorteile zum einen in einer geringeren Bodenverdichtung und zum anderen in einer höheren Laufruhe der Maschine liegen, die besonders bei sehr breiten Schneidwerken von Bedeutung ist. Durch die Auslegung eines Mähdreschers als Hecklenker kann mit dem unmittelbar vor der Vorderachse montierten Schneidwerk ein sehr enger Wendekreis erreicht werden.
Da die optimale Fahrgeschwindigkeit beim Dreschen von vielen Faktoren abhängt (Motorleistung, Dreschverluste, Bestandsdichte, Lagergetreide, Bodenunebenheiten etc.), ist es wichtig, dass die Geschwindigkeit des Mähdreschers stufenlos verändert werden kann. Dazu dienen meist Variator- oder hydrostatische Getriebe.
Fahrerkabine
Anstelle des bei frühen Mähdreschern gängigen offenen Fahrerplatzes direkt hinter dem Schneidwerk und über dem Schrägförderer mit erheblicher Staub-, Lärm- und bei entsprechender Witterung Hitzebelastung des Maschinenführers ist bei modernen Mähdreschern fast ausnahmslos an gleicher Stelle eine geschlossene Fahrerkabine aufgebaut. Diese erlaubt einen wirksamen Schutz des Fahrers vor Staub, Lärm und Hitze und ist daher in der Regel klimatisiert und komfortabel für einen langen Arbeitstag (meist zwischen 10 und 14 Stunden) ausgeführt. Sie enthält auch die elektronischen Steuerungen und Anzeigen zur Einstellung und Überwachung aller relevanten Parameter des Mähdreschers (Motoranzeigen, Steuerung des Schneidwerks und des Dreschwerks, immer öfter Instrumente zur Ertragsmessung, teilweise kombiniert mit GPS-Erfassungssystemen).
Die Steuerung des Schneidwerks, des Abtankrohrs und der Fahrgeschwindigkeit wird mit einem Hebel durchgeführt, welcher ständig in der rechten Hand des Fahrers geführt wird (die linke Hand liegt am Lenkradknauf). Bei modernen Mähdreschern ist dies ein Joystick, der die Elektronik ansteuert. In älteren Modellen ist ein Hebel mit den Hydrauliksteuergeräten mechanisch verbunden. Durch Wahl der Hebelgasse wird die Funktion des Steuergeräts (Schneidwerkshöhe, Abstand Haspel/Schneidwerkstisch, Fahrgeschwindigkeit) gewählt. Weitere Hebelgassen können beispielsweise für Haspelgeschwindigkeit oder Dreschtrommeldrehzahl vorhanden sein, sind meist aber erst nach Lösen einer Sicherung zugänglich, um versehentliches Verstellen zu verhindern.
Automatisierung
In den letzten Jahren werden vermehrt Steuerungs- und Kontrollaufgaben, die früher durch den Fahrer ausgeführt wurden, von automatisierten Einrichtungen übernommen. So wird beispielsweise das Schneidwerk auf einer vom Fahrer vorgegebenen Schnitthöhe automatisch den Geländeunebenheiten nachgeführt. Sensoren erfassen die Bodenunebenheiten, entsprechend den Sensordaten verändert die automatisierte Steuerung sodann Arbeitshöhe sowie Neigung des Schneidwerks. Ein weiterer Automatisierungsschritt sind selbsttätige Lenksysteme. Durch DGPS kann die Position des Mähdreschers auf dem Feld mit einer Genauigkeit von ± 10 cm bestimmt werden. Mit diesen Informationen führt der Bordcomputer den Mähdrescher parallel entlang der vorherigen Fahrspur über das Feld. Der Fahrer braucht das Steuer nur noch am Ende des Feldes in die Hände zu nehmen, um die Maschine zu wenden. Auch gibt es Systeme, die mit Sensoren die Menge des Dreschgutes messen und die Geschwindigkeit des Mähdreschers so anpassen, dass dieser immer mit optimaler Auslastung fährt.
Geschichte
Bis zur Mechanisierung der Landwirtschaft wurde Getreide von Hand – wenn die gallo-römische Mähmaschine (vallus), die mit dem Ende der Antike verschwand, außer Acht gelassen wird – in mehreren Arbeitsschritten geerntet. Zuerst mähte man das Getreide mit Sichel, Sichte oder Sense ab und band es in der Regel zu Garben, die zunächst auf dem Feld stehen blieben. Gemäht wurde bereits vor der beim Mähdrusch erforderlichen Totreife des Getreides; das auf dem Feld in Garben aufgestellte Erntegut reifte dort noch nach und trocknete, sodass bei der Mahd weder Korn noch Stroh die notwendige Trockenheit zur Endlagerung haben mussten. In der Regel transportierte man die Garben dann zum Bauernhof, um das Getreide – oft nach weiterer Lagerung – in der Scheune auf der Tenne mit Dreschflegeln auszudreschen. Anschließend reinigte man es durch Sieben oder Worfeln von der Spreu und Verunreinigungen wie Erde oder Unkrautsamen. Beim Worfeln wurden leichte Bestandteile des hochgeworfenen Druschs wie die Spreu vom Wind weggeweht. Später wurden dafür einfache handbetriebene Windfegen verwendet, bei denen ein Siebkasten das Getreide in einen darunter angebrachten Windkasten rieseln ließ; diese Windsichtung ist bis heute Bestandteil der Reinigungsstufe von Mähdreschern.
Mit der einsetzenden Mechanisierung wurden etwa ab 1786 zunächst stationäre Dreschmaschinen entwickelt, die anfangs von Hand oder über Göpel von Tieren angetrieben wurden. Später wurden Dampfmaschinen, Verbrennungsmotoren, Elektromotoren und andere Antriebe eingesetzt. Die erste Mähmaschine für Getreide entwickelte 1826 der schottische Geistliche Reverend Patrick Bell. Mit der Erfindung des mechanischen Knoters 1857 wurde es möglich, Mähbinder zu bauen, die das Getreide vollmechanisiert zu Garben banden. Zunächst wurden diese Maschinen von Pferden gezogen und dabei über die Maschinenräder angetrieben. Mit Erscheinen brauchbarer Traktoren nutze man zunächst auch sie anstelle von Pferden zum Zug. 1927 produzierte Krupp einen ersten Mähbinder, der unmittelbar über eine Zapfwelle vom Motor des Traktors angetrieben wurde.[6]
Aus der Kombination von Mähmaschine und fahrbarer Dreschmaschine entstanden die ebenfalls mobilen Mähdrescher. Bereits 1834 führten Hiram Moore und James Hascall in Michigan eine Maschine vor, die sowohl mähen und dreschen als auch reinigen konnte; die Arbeitsbreite betrug 4,60 Meter.[7] 1836 wurde die Maschine patentiert. Bis zu 40 Maultiere oder Pferde waren erforderlich, um diese Maschinen zu ziehen. Die Dresch- und Reinigungsorgane wurden über eines der Räder angetrieben. George Stockton Berry baute 1886 den ersten selbstfahrenden Mähdrescher, der von einer Dampfmaschine angetrieben wurde. Der Kessel wurde mit dem ausgedroschenen Stroh befeuert und versorgte auch den separaten Antrieb der Dreschorgane mit Dampf.[8] 1911 verwendete die Holt Manufacturing Company in Stockton, Kalifornien erstmals Verbrennungsmotoren auf Mähdreschern; sie trieben jedoch nur Dresch-, Abscheide- und Reinigungssystem an und noch nicht das Fahrwerk.
Der erste selbstfahrende Mähdrescher eines deutschen Herstellers war der MD 1 der Maschinenfabrik Fahr; er wurde auf der DLG-Ausstellung in Hamburg im Jahr 1951 erstmals der Landwirtschaft präsentiert. Zu Beginn der 1950er-Jahre spielten gezogene Mähdrescher in Deutschland noch eine große Rolle. Erfolgreiche Mähdrescher wie der Lanz MD 50, der IHC D61 und der MF 30 wurden für etwa 10.000 DM verkauft. Während des Schlepperbooms gab es in Deutschland zeitweilig 12 Mähdrescherhersteller, die sich am Markt jedoch nicht alle durchsetzen konnten. Als Erntemaschine war der Mähdrescher ab den 1970er-Jahren etabliert.[9] Ein erster Rotormähdrescher wurde von New Holland im Jahr 1975 auf den Markt gebracht.
-
Stereofotografie (veröffentlicht 1902) eines durch Zugtiere angetriebenen Mähdreschers
-
Getreideernte mit einem Stalinez 4 (1953)
-
Reparatur eines Mähdreschers (1961)
Mähdreschertypen
Mähdrescher werden nach der Fortbewegungsart und nach der Arbeitsweise unterschieden.
Fahrantrieb
Nach der Art der Fortbewegung unterscheidet man Selbstfahrer mit eigenem Antrieb und durch Zugtiere oder Traktoren gezogene Geräte. Bei den gezogenen Maschinen gibt es neben Geräten mit Antrieb der Schneide- und Dreschorgane über die Zapfwelle des Traktors auch solche, bei denen diese durch einen separaten Verbrennungsmotor (Aufbaumotor) angetrieben werden, die Zugmaschine bzw. die Zugtiere haben dann lediglich das Gerät über das Feld zu bewegen.[10]
-
Selbstfahrender Mähdrescher bei der Arbeit
-
Gezogener Mähdrescher
Arbeitsweise der Dreschorgane und Abscheidung
Nach der Arbeitsweise unterscheidet man in drei Kategorien:
- Konventioneller Mähdrescher mit Dreschtrommel und Hordenschüttler s. Schemazeichnung oben
- Axialmähdrescher ohne Dreschtrommel – nur Rotoren erledigen den Drusch und die Abscheidung
- Hybrid-Mähdrescher mit Dreschtrommel und Rotor
Das eigentliche Druschsystem besteht aus einer Dreschtrommel und einem Dreschkorb. Hierbei werden vier grundlegende Konzepte unterschieden.
Tangentiales Dreschsystem (konventionell)
Die Achse der Dreschtrommel liegt quer zur Fahrtrichtung im Mähdrescher. Der Fluss des Erntegutes ist darum tangential zur Trommel. Je nach Leistungsanforderung werden zwei oder mehr sich drehende Aggregate eingebaut. Tangentiale Aggregate werden nie mehr als eine dreiviertel Umdrehung vom Stroh umschlungen. Danach verlässt das ausgedroschene Stroh wieder die Trommel. Auf diesem kurzen Weg fallen nicht alle Körner durch den Dreschkorb. Also wird ein weiteres Abscheidesystem benötigt.
Axiales Dreschsystem
Bei axialen Dreschaggregaten verläuft die Drehachse des Rotors in Fahrtrichtung. Das Stroh wird mehrfach um den Rotor herumgeführt. Schräg angeordnete Bleche an der oberen Innenseite der Rotortrommel bewirken den Schub nach hinten. Daher ist die Hauptflussrichtung des Erntegutes entlang der Achse.
Der Drusch findet im vorderen Abschnitt des Rotors statt, die Abscheidung im hinteren Teil. Es muss ein Kompromiss zwischen Dreschdrehzahl und Abscheidedrehzahl gefunden werden. John Deere arbeitet hier mit unterschiedlichen Rotor/Gehäusedurchmessern im Gutverlauf. Ein russischer Hersteller verwendet rotierende Körbe. Die Abscheideleistung von Rotoren ist sehr hoch. Verluste steigen nicht so stark mit Erhöhung des Durchsatzes an, wie bei der Schüttlerabscheidung.
Aufgrund der wesentlich einfacheren Bauweise und des daraus resultierenden Kostenvorteils hat sich diese Bauweise in Nord- und Südamerika sowie in Russland durchgesetzt. Bei den dort herrschenden günstigen Dreschbedingungen lassen sich Durchsätze erreichen, die nur unwesentlich unter denen von Hybridsystemen und deutlich über denen von tangentialen Systemen liegen.
Das Stroh wird mechanisch stark beansprucht und lässt sich daher fast nicht als Langstroh weiterverarbeiten.
Transversales Dreschsystem
Funktionell ist das transversale Dreschsystem ähnlich dem axialen Dreschsystem. Es wird ebenfalls ein Rotor zum Drusch und zur Abscheidung genutzt. Die Drehachse liegt jedoch quer im Mähdrescher. Somit muss das Druschgut nicht in seinem natürlichen Fluss umgelenkt werden, wie dies bei der Zuführung eines Axialrotors geschieht. Im Unterschied zur Dreschtrommel wird das Erntegut mehr als eine ganze Umdrehung im Rotor mitgeführt. Das transversale Dreschsystem wird überwiegend bei spezialisierten Kleinmähdrescher für den Reisdrusch (z. B. Claas Crop Tiger) verbaut. Bei herkömmlichen Mähdreschern wird das System nur von AGCO-Gleaner angeboten.
Hybride Dreschsysteme
Beim hybriden Druschsystem wird das Dreschgut in einer oder mehreren tangentialen Dreschtrommeln gedroschen und danach zu einem oder mehreren Abscheiderotoren geführt. Der Abscheiderotor hat gegenüber dem Schüttler den Vorteil, dass er eine wesentlich intensivere Trennung von Spreu und Stroh ermöglicht. Nachteilig ist, dass dabei das Stroh mehr beansprucht wird und Strohbruch die Reinigung stärker belastet. Daher ist die Reinigung bei vielen Modellen der begrenzende Faktor. Aus diesem Grund muss die Drehzahl der Abscheiderotoren den Erntebedingungen angepasst werden, um einen Kompromiss zwischen Abscheidungs- und Reinigungsleistung zu finden.
Abscheidesysteme
Bei der Abscheidung unterscheidet man zwischen zwei grundsätzlich verschiedenen Arten von Abscheideorganen.
- Hordenschüttler: Bei herkömmlichen Mähdreschern erfolgt die Abscheidung über einen Hordenschüttler. Der Schüttler besteht aus vier bis sechs Horden, auf deren Oberseite widerhakenförmige Zacken angebracht sind. Alle Horden sind an zwei Kurbelwellen befestigt, die sich drehen. Es ergibt sich eine kreisförmige Exzenterbewegung der Horde: zuerst nach oben, dann nach hinten, dann nach unten, dann nach vorne. Wenn eine Horde am obersten Punkt ist, sind die daneben liegenden Horden am tiefsten. Auf dem Weg nach oben übernehmen die Horden so die Strohmatte von den daneben liegenden und führen sie mit den Widerhaken nach hinten. Bei der Abwärtsbewegung geben sie die Matte wieder an die daneben liegenden Horden ab. Leer laufen sie wieder in Fahrtrichtung nach vorne.
Dadurch wird das Stroh so aufgeworfen, dass die noch mitgeführten Körner durch die Strohmatte hindurchfallen. Unter jeder Horde ist eine Wanne, auf der die Körner schräg nach vorne auf den Vorbereitungsboden laufen.
Der Schüttler ist jenes Abscheidesystem, welches das Stroh am wenigsten beansprucht und zerstört. Bei feuchtem oder unreifem Stroh sinkt die Abscheideleistung schnell. Bei der Fahrt bergauf steigen die Verluste ebenfalls, weil die Hangneigung der Schüttlerneigung entgegensteht. Am Seitenhang begrenzt die Horde an der Hangunterseite die Abscheideleistung. Unter diesen Bedingungen muss die Fahrgeschwindigkeit reduziert werden.
- Axiale Abscheideelemente: Mähdrescher mit sehr breiten Schneidwerken werden darum mit axialen Abscheideelementen gebaut. Ein oder zwei (dann nebeneinander angeordnete) axiale Rotoren übernehmen die Aufgabe der Abscheidung. Durch die Fliehkräfte werden Korn und Stroh voneinander getrennt. Elemente aus einer Korbstruktur, die den Rotor mindestens unterhalb umschließen, verhindern, dass zu viele Nichtkornbestandteile auf die Reinigung gelangen und somit deren Funktionsfähigkeit einschränken. Bei axialen Systemen passiert das Stroh die Abscheidung rund zehnmal schneller als bei Schüttlersystemen. Daher sind größere Durchsätze möglich und vor allem bei feuchten Erntebedingungen ist der Kornverlust erheblich geringer. Axialmähdrescher sind zudem weniger anfällig gegen starke Hangneigungen, da hier die Schwerkraft weniger Bedeutung für die Abscheidung hat.
Hangmähdrescher
Getreide wird in aller Regel auf ebenen Flächen angebaut. Es gibt jedoch Regionen, wo auch in sanft hügeligen bis zum Teil recht steilen Topografien Druschfrüchte angebaut werden. Wie oben beschrieben, wird der Drusch- und Trennprozess in Mähdreschern sehr stark von der Topografie oder eben der Schwerkraft beeinflusst. Bereits die durch die Hangneigung einseitige Beschickung des Dreschwerkes reduziert die Leistungsfähigkeit der Maschine enorm, da nicht die ganze Dreschwerksbreite genutzt wird. Schlimmer jedoch ist die einseitige Beschickung der Reinigungsanlage (Vorbereitungsboden, Siebe) mit dem ausgedroschenen Gut. Spreu und Korn erreichen die Reinigungsanlage auf der hangabwärts liegenden Seite, darüber hinaus wird durch die Siebbewegung das Material weiter einseitig konzentriert.
Die Leistungseinbuße steigt exponentiell mit der Hangneigung. Es ist also von großem Interesse, die Hangneigung resp. diese Leistungseinbuße zu kompensieren. Dazu existieren verschiedene Systeme.
Hangfahrwerk

Ältestes Verfahren, das heute vor allem bei extremen Hanglagen noch immer angewandt wird, ist, dass das Fahrwerk so angehoben oder abgesenkt wird, dass die Dreschorgane waagerecht liegen. Der erste Mähdrescher mit einem Hangausgleich nach diesem Prinzip wurde 1891 von den Gebrüdern Holt in Kalifornien gebaut.[11] Der Hangausgleich musste bei früheren Maschinen mechanisch eingestellt werden, wofür eine zweite Person auf dem Mähdrescher notwendig war. Der erste automatische Hangausgleich wurde 1941 von Raymond A. Hanson entwickelt. 1945 stattete er die ersten Maschinen mit diesem System aus, bei dem der Grad der Neigung über Quecksilberschalter ermittelt wurde, und die Abscheideorgane über pneumatische Zylinder entsprechend ausgerichtet wurden.[12]
Heute geschieht der Ausgleich in der Regel mittels zweier Hydraulikzylinder, die den Mähdrescher einseitig von der Vorderachse abheben und somit waagerecht halten. Da die Hinterachse pendelnd gelagert ist, ist hier kein Neigungsausgleich erforderlich. Seltener ermöglicht eine Hubhydraulik an der Hinterachse auch einen Neigungsausgleich in Längsrichtung.
Problematisch ist hier der technische Aufwand und die damit verbundenen Kosten. Auch die Gutübergabe vom schrägen Schneidwerk auf den geraden Mähdrescher ist problematisch. Dieses System bietet jedoch den Vorteil, dass das komplette Fahrzeug mit Ausnahme des Schneidwerks in der Waagerechten gehalten wird. Somit wird die Leistung der Reinigungsorgane nicht durch die Seitenlage beeinträchtigt. Auch kann so das Volumen des Korntanks voll ausgenutzt werden, was nicht möglich ist, wenn das Fahrzeug zur Seite geneigt ist, da das Erntegut zu dieser Seite verrutschen würde, was in extremen Fällen sogar ein Umkippen des Fahrzeugs zur Folge haben kann. Darüber hinaus erhöht sich der Fahrkomfort, da auch der Fahrer in einer geraden Sitzposition verbleibt, und nicht aus dem Sitz zu rutschen droht.
Querbleche
Als weiteres sehr einfaches System haben sich Querbleche auf den Sieben durchgesetzt die das Gut nur bedingt zur Hangseite rutschen lassen.
Hangausgleich
Als weitere Lösung setzt Claas auf einen Hangausgleich. Dabei wird die Hangneigung gemessen und die Siebe über einen Hydraulikaktor in eine von der Neigung abhängige Querschwingung versetzt. Hierdurch wird das Gut gegen die Schwerkraft hangaufwärts gefördert und so gleichmäßig verteilt. Ebenfalls werden von New Holland Hangausgleichsysteme angeboten, welche je nach Hangneigung, die über eine elektronische Wasserwaage festgestellt wird, mittels eines elektrischen Spindelmotors die gesamte Reinigung (Siebkasten und Gebläse) in waagerechter Position halten. Beide Systeme gleichen lediglich Querneigungen der Maschine aus.
Rotormähdrescher
Bei Rotormähdreschern haben Schräglagen am Hang keinen nennenswerten Einfluss auf die Restkornabscheidung, da diese rotatorisch statt durch lageabhängig arbeitenden Schüttler stattfindet. Da die Reinigung in der Regel konventionell als Siebkasten ausgeführt ist, werden Rotormähdrescher ebenfalls mit Hangausgleich angeboten.
Hersteller

Die in den letzten Jahren in vielen Bereichen stattfindende Unternehmenskonzentration ist auch auf dem Agrar-Sektor zu beobachten. Bei Mähdreschern tragen zusätzlich die hohen technologischen Anforderungen sowie die kapitalintensive Produktion dazu bei, dass viele früher eigenständige Unternehmen heute in einem Dachkonzern vereinigt sind. Dabei werden etablierte Markennamen teilweise nebeneinander beibehalten oder – etwa regional oder im Produktspektrum – differenziert. Während weniger bekannte oder angesehene Marken aufgegeben werden, können Unternehmen mit hochwertigem Image bisher nicht vorhandene Produktlinien unter eigenem Namen von Konzernschwestern übernehmen.
Die Weltmarktführer auf dem Mähdreschersektor sind (Stand: 2022):[13]
- Claas, ein nicht börsennotiertes deutsches Familienunternehmen
- John Deere, zugleich der Weltmarktführer bei Landmaschinen insgesamt
- Zhengzhou Amisy Machinery Co. Ltd., aus China
- Yanmar (Japan).
- Kubota (Japan)
Weitere große Hersteller von Mähdreschern:
- Im CNH-Industrial-Konzern, weltweit an zweiter Stelle der Landmaschinenproduzenten, ging unter anderem die DDR-Marke Fortschritt auf; heutige Marken sind
- Case IH und
- New Holland.
- Die 1990 entstandene AGCO (Allis-Gleaner Corporation) vereinigt einige bekannte Marken:
- Gleaner war von Beginn an der Markenname für Erntemaschinen.
- Massey Ferguson wurde 1994 übernommen.
- Fendt kam 1997 zum Konzern und bietet seit 1999 Mähdrescher unter eigenem Namen an.
- Laverda ist seit 2010 im hundertprozentigen Konzernbesitz.
- SDF verkauft Mähdrescher unter der Marke Deutz-Fahr und ist damit das Nachfolgeunternehmen des ersten deutschen Produzenten. Die Produktion von Mähdreschern im Werk in Kroatien wird 2025 eingestellt.
- Gomselmash ist ein belarussischer Hersteller von (u. a.) Mähdreschern.
- Rostselmasch ist ein russischer Hersteller von (u. a.) Mähdreschern.
- Sampo Rosenlew ist ein finnischer Hersteller von (u. a.) Mähdreschern.
Parzellendrescher für das Versuchswesen stellt die Firma Zürn Harvesting[14] her, die die Firma des Erfinders dieses Mähdreschertyps, Hans-Ulrich Hege, aufgekauft hat[15]. Ein weiterer Hersteller für diesen Spezialsektor ist Wintersteiger.[16]
Trivia
Auf der Rückseite der 5-DDR-Mark-Banknoten war ein Mähdrescher vom Typ Fortschritt E 512 abgebildet.
Literatur
- Udo Bols: Mähdrescher in Deutschland 1931 bis heute. 3 Bände, Podszun, Brilon 2005–2008, ISBN 978-3-86133-406-4.
- Dr. Klaus Krombholz, Dr. Hasso Bertram und Hermann Wandel: 100 Jahre Landtechnik – von Handarbeit zu High-Tech in Deutschland. DLG-Verlag, Frankfurt am Main, 2009, ISBN 978-3-7690-0737-4.
- Graeme R. Quick, Wesley F. Buchele: The Grain Harvesters. American Society of Agricultural Engineers, St. Joseph/Michigan 1978, ISBN 0-916150-13-5.
- Manfred Baedecker, Ralf Lenge: Die Claas Mähdrescher Story. Landwirtschaftsverlag, Hiltrup 2001, 2. Auflage 2003. ISBN 3-7843-3053-3.
- Ralph Vogelding, Lohndreschbetriebe und Maschinendrusch, Coppenrath Verlag, 1989, PDF-Online mit 400 Seiten bei lwl.org.
Weblinks
- Literatur von und über Mähdrescher im Katalog der Deutschen Nationalbibliothek
- Funktionsweise eines Mähdreschers, auf bauernhof.net, abgerufen am 5. Oktober 2021
- Funktionsweise eines Mähdreschers (Video)
- Animation eines Mähdreschers (Video)
Einzelnachweise
- ↑ Paul Schweigmann: Die Landmaschinen und ihre Instandhaltung. 1. Auflage, Pfanneberg, Gießen 1955, Nachdruck durch Bulldog-Press, Limburg a. d. Lahn 1993, ISBN 3-9803332-1-3, S. 196–197
- ↑ Horst Eichhorn, Landtechnik, 7. Auflage, Ulmer, Stuttgart, 1952, 1999, ISBN 3-8001-1086-5, S. 259 f.
- ↑ Erntestudie. In: Dragotec. 5. August 2020, abgerufen am 7. Mai 2021 (deutsch).
- ↑ Fendt Ideal Technische Daten. ( vom 2. August 2019 im Internet Archive) AGCO / Fendt, 2. August 2019
- ↑ Claas Lexion 8000. Claas, 2. August 2019
- ↑ http://www.cornways.de/hi_combine.html
- ↑ Archivierte Kopie ( vom 29. September 2008 im Internet Archive)
- ↑ Archivierte Kopie ( vom 29. September 2008 im Internet Archive)
- ↑ M. Baedecker, R. Lenge, S. 13 + 14
- ↑ Paul Schweigmann, Die Landmaschinen und ihre Instandhaltung, 1. Auflage, Pfanneberg, Gießen, 1955, Nachdruck durch Bulldog-Press, Limburg a. d. Lahn, 1993, ISBN 3-9803332-1-3, S. 280 ff.
- ↑ Archivierte Kopie ( vom 29. September 2008 im Internet Archive)
- ↑ Archivierte Kopie ( vom 29. September 2008 im Internet Archive)
- ↑ Combine Harvesters Market Share, Report, Analysis 2022 - 27. Abgerufen am 10. November 2022 (englisch).
- ↑ www.zuern.de
- ↑ Firma Zürn übernimmt die Produktion der Parzellendrescher von Hege ( vom 19. Juli 2016 im Internet Archive)
- ↑ www.wintersteiger.com (Seite nicht mehr abrufbar, festgestellt im Mai 2019. Suche in Webarchiven)
License Information of Images on page#
Image Description | Credit | Artist | License Name | File |
---|---|---|---|---|
Claas-Traktor Atles 946 RZ und Mähdrescher Mega 360 auf der Belagro 2007 in Minsk | Photo made by EugeneZelenko 's mother, Hanna Zelenko | Hanna Zelenko | Datei:Belarus-Minsk-Agriculture Expo-Mega 360.jpg | |
Es folgt die historische Originalbeschreibung , die das Bundesarchiv aus dokumentarischen Gründen übernommen hat. Diese kann allerdings fehlerhaft, tendenziös, überholt oder politisch extrem sein. Schwoitsch, Getreideernte mit Mähdrescher, Gerste Zentralbild Gerbeth 3.7.1953 Ernte in der Deutschen Demokratischen Republik Im Saalkreis des Bezirks Halle ist die Ernte im vollen Gange. Eine große Hilfe und Erleichterung bringen die sowjetischen Erntemaschinen, die auch auf den Feldern des Saalkreises eingestzt sind. UBz: Kollegen der MTS Gröbers ernten mit dem "Stalinez 4" die Wintergerste auf den Feldern der Genossenschaft in Schwoitsch. Am Steuer der zweifache Aktivist Liebtal. Leihweise Zentral Bild x | Dieses Bild wurde im Rahmen einer Kooperation zwischen dem deutschen Bundesarchiv und Wikimedia Deutschland aus dem deutschen Bundesarchiv für Wikimedia Commons zur Verfügung gestellt. Das deutsche Bundesarchiv gewährleistet eine authentische Bildüberlieferung nur durch die Originale (Negative und/oder Positive), bzw. die Digitalisate der Originale im Rahmen des Digitalen Bildarchivs . | Gerbeth | Datei:Bundesarchiv Bild 183-20193-0003, Schwoitsch, Getreideernte mit Mähdrescher, Gerste.jpg | |
Es folgt die historische Originalbeschreibung , die das Bundesarchiv aus dokumentarischen Gründen übernommen hat. Diese kann allerdings fehlerhaft, tendenziös, überholt oder politisch extrem sein. Barnitz, Reparatur eines Mähdreschers Zentralbild Siegert Kä-Qu13.2.1961 Reparatur in der MTS Barnitz. Die MTS Barnitz im Kreis Meisen übernahm die Mähdrescherrepatatur von drei MT-Stationen. Bis zum 15.4. wird die Reparaturbrigade, zu der 16 Mitglieder zählen, 28 Mähdrescher im Taktsystem überholen. UBz: Reparatur eines Mähdreschers. | Dieses Bild wurde im Rahmen einer Kooperation zwischen dem deutschen Bundesarchiv und Wikimedia Deutschland aus dem deutschen Bundesarchiv für Wikimedia Commons zur Verfügung gestellt. Das deutsche Bundesarchiv gewährleistet eine authentische Bildüberlieferung nur durch die Originale (Negative und/oder Positive), bzw. die Digitalisate der Originale im Rahmen des Digitalen Bildarchivs . | Horst Siegert | Datei:Bundesarchiv Bild 183-80260-0001, Barnitz, Reparatur eines Mähdreschers.jpg | |
CASE combine harvester Axial-Flow 2388 X-Clusive | https://www.flickr.com/photos/xenithorg/52926611/ | https://www.flickr.com/photos/xenithorg/ | Datei:CASE combine harvester.jpg | |
Case 7010 combine harvesting rape | originally posted to Flickr as 2009-09-13 2-06-58 PM_0201 | Warren Long | Datei:Case 7010 field.jpg | |
koeris using harvester | Transferred from Wikipedia: en.wikipedia.org 1 : 2004-09-16 14:05 . . Hinrich . . 800x600 (132778 bytes) . . (Claas Lexion 570, GFDL) de.wikipedia.org 2 : 2004-07-17 20:53 . . Hinrich . . 800 x 600 (132778 Byte) . . (Claas Lexion 570, CC-by-sa-2.0-de) | Hinrich | Datei:Claas-lexion-570-1.jpg | |
Bedienhebel eines Claas Dominator 68, Baujahr 1996 | Eigenes Werk | Blonder1984 | Datei:Claas Dominator Bedienhebel.JPG | |
Claas Lexion 405 mit Klappschneidwerk | Flickr as charrue faucheuse rateleuse fleurie Claas Lexion Coupe Repliable | Leroy-Jovial Car- 70 années avec Neoplan-Setra-Me | Datei:Claas Lexion 405 a.jpg | |
Claas Lexion 760 Mähdrescher | Eigenes Werk | Nxr-at | Datei:Claas Lexion 760 Mähdrescher.jpg | |
A Claas Mercator's rye seperator („Halmteiler“) | Eigenes Werk | Johannes Maximilian | Datei:Claas Mercator JM 2023 08 11 5D410104.jpg |